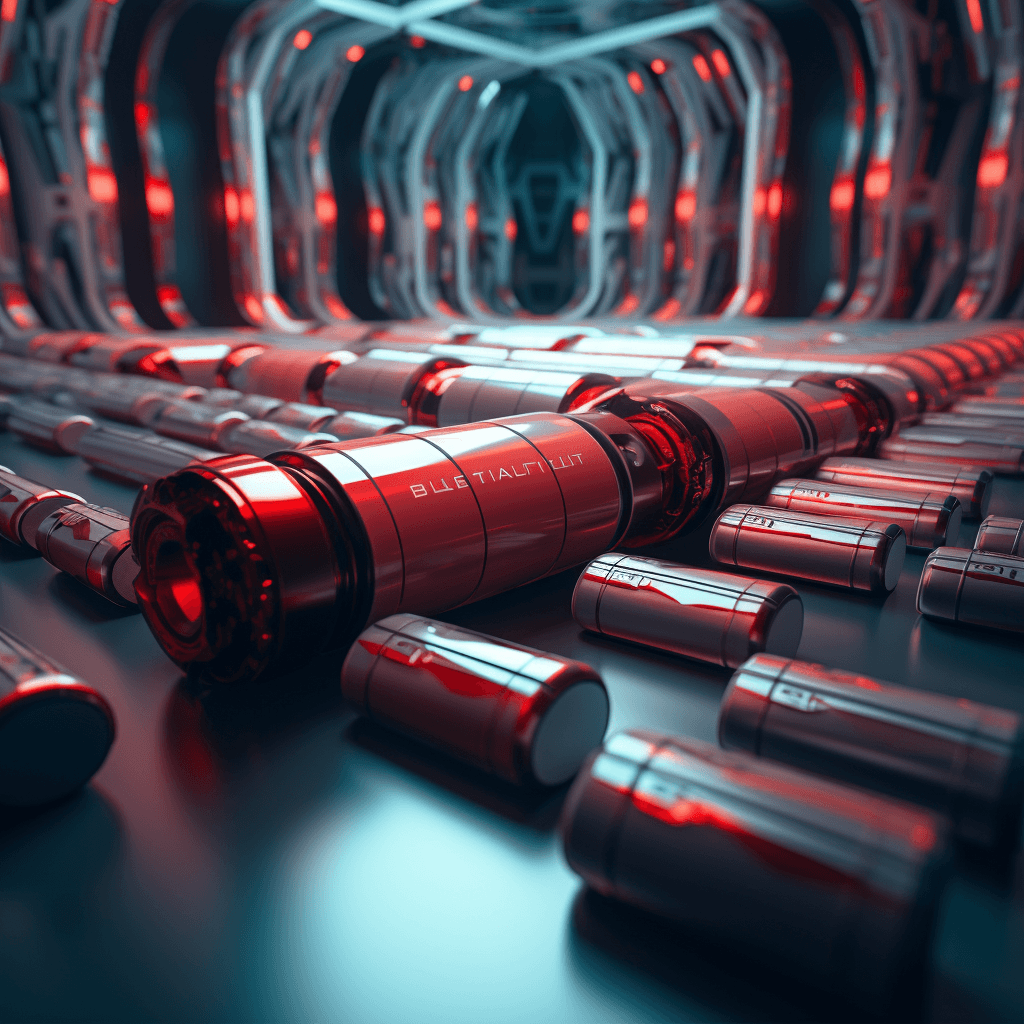
Supercharging Battery Manufacturing for the Future
Share
Batteries play a crucial role in powering our daily lives. From smartphones to electric vehicles, our modern technological conveniences would not be possible without advanced battery systems. As demand for batteries grows, manufacturers are continually seeking ways to optimize production to increase performance, lower costs, and keep up with market needs.
By implementing improvements in manufacturing processes, exploring new materials, and adopting cutting-edge technologies, battery production can become more efficient, environmentally-friendly, and yield products with better capabilities. This article will examine the current state of battery manufacturing and opportunities for advancing the field to meet future performance requirements.
Current Battery Manufacturing Methods
Most modern batteries rely on lithium-ion technology and consist of an anode, cathode, electrolyte, and separator. Common anode materials include graphite and silicon, while cathodes are typically made from lithium compounds like lithium cobalt oxide. The electrolyte carries charged lithium ions between the electrodes, generating electricity.
To produce lithium-ion batteries, manufacturers must carefully control production processes like electrode fabrication, cell assembly, electrolyte filling, and packaging. The electrodes are coated with active materials using techniques like vapor deposition or mixing with binders. Cells are assembled by stacking alternating cathode and anode layers with separators in between. The liquid electrolyte is then injected into the battery cell casing, which is sealed.
Quality control steps are implemented throughout manufacturing. Cells are tested for electrical performance, measured for physical dimensions, and inspected for defects. Advanced analytical techniques like x-ray computed tomography can also be used to evaluate internal battery structure.
Areas for Improvement in Battery Manufacturing
While current manufacturing methods have improved markedly over the years, there are still areas for potential enhancement:
- Reducing batch-to-batch variability and improving product consistency
- Increasing yield and minimizing scrap/waste
- Shortening production timelines to meet growing market demand
- Lowering equipment and operating costs
- Maximizing battery performance attributes like energy density, cycle life, and safety
New manufacturing approaches can help address these pain points. Strategies like process modeling, automation, and advanced quality control can optimize production. Designing equipment and workflows for flexibility allows manufacturers to quickly shift between products.
Emerging Battery Chemistries and Materials
An important aspect of next-generation battery manufacturing is developing new chemistries and materials. Lithium-ion batteries currently dominate, but alternatives are being researched to push past limitations:
-
Lithium-sulfur batteries offer high theoretical energy density and use inexpensive sulfur at the cathode. However, challenges remain in optimizing morphology and preventing cathode dissolution.
-
Lithium-air batteries utilize oxygen from the air instead of a traditional cathode. This provides exceptionally high energy density, but issues around stability and reusable need resolution.
-
Solid-state lithium-ion batteries replace liquid electrolytes with solid materials to improve safety and energy density. Manufacturing processes must be refined to enable thin, uniform solid electrolytes.
-
Multivalent ion batteries using magnesium or aluminum at the anode provide benefits like enhanced safety and faster charging. Manufacturing methods tailored to these new chemistries will be important.
Mastering the production of novel batteries will allow manufacturers to meet demanding performance requirements.
Advanced Manufacturing Techniques
Several sophisticated techniques available today can help upgrade battery manufacturing:
-
Additive manufacturing via 3D printing enables greater design flexibility. It allows rapid prototyping and small-batch production of intricate or optimized battery components.
-
In-line monitoring tools like machine vision track batteries through production, automatically catching flaws. This improves quality control and reduces waste.
-
Laser-based processes can precisely cut, drill, weld, and structurally modify battery materials at small scales. Lasers are finding increasing uses in battery fabrication.
-
Nanoscale surface engineering modifies battery materials at microscopic scales to enhance properties like charge transfer and ion transport. Controlled manipulation at such small dimensions is crucial.
Adapting these kinds of emerging technologies for battery manufacturing will drive significant improvements in product performance, consistency, and customizability moving forward.
Automation and Robotics in Battery Production
Greater implementation of automation and robotics has enormous potential to optimize battery manufacturing. Robotic arms equipped with specialized tools can take over manual, repetitive production tasks with enhanced speed, precision, efficiency and consistency.
Automated guided vehicles can smoothly transport materials between workstations without errors. Automated inspection systems can meticulously examine batteries for defects. By minimizing direct human involvement in manufacturing, variability is reduced and output volumes can be scaled up.
Artificial intelligence can also be applied to production controls, monitoring equipment performance, adjusting operating parameters, and predicting maintenance needs. With the growing demand for batteries, automated and robotic systems will become essential assets in achieving high-volume, economical production.
Quality Control and Testing
Rigorous quality control and testing ensures optimal battery performance, safety, and reliability. Throughout production, battery samples at various stages undergo thorough analytical characterization and evaluation.
Standard tests assess key metrics like voltage, capacity, impedance, power capability, cycle lifetime, and temperature stability. Environmental testing exposes batteries to stresses like humidity, vibration, and shock to confirm resilience. Abuse testing deliberately damages batteries to understand failure modes and margins of safety.
State-of-the-art facilities allow batteries to be evaluated under precisely controlled conditions. Maintaining stringent quality standards through comprehensive testing and analysis is vital to releasing products ready for consumer applications.
Sustainable and Eco-Friendly Manufacturing
With rising concern about environmental impacts, sustainable manufacturing practices are an increasing priority in the battery industry. This covers minimizing waste, efficiently utilizing resources, reducing emissions, recycling materials, and ensuring worker safety.
Production process improvements coupled with greater use of automation/robotics conserves resources and provides a cleaner working environment. Some emerging battery chemistries utilize abundant, non-toxic materials. Newly developed water-based manufacturing techniques avoid hazardous solvents.
Recycling battery materials like cobalt and lithium back into production loops will also become essential. By taking environmental considerations into account, battery manufacturing can limit its ecological footprint. This will only grow in importance going forward.
Future Outlook for Battery Manufacturing
The field of battery manufacturing is on the cusp of major changes driven by urgent market demands, disruptive technologies and materials, automated and optimized production, and sustainability concerns.
With electric vehicles and energy storage projected as pivotal to our energy future, battery production capacity must swell dramatically while also delivering better performance at lower prices. Breakthrough manufacturing advances in areas like additive processes, advanced quality control, and recycling will be instrumental in achieving these goals.
Harnessing techniques from parallel industries like semiconductor fabrication can also catalyze progress. Ultimately, meeting future energy storage needs will require battery manufacturing to become vastly more efficient, flexible, high-volume, and economical while maintaining exacting quality standards. Ongoing innovation toward these objectives has excellent prospects for transforming this vital sector.